Robotic PFS Filling And Closing Machine
Robotic PFS Filling And Closing Machine
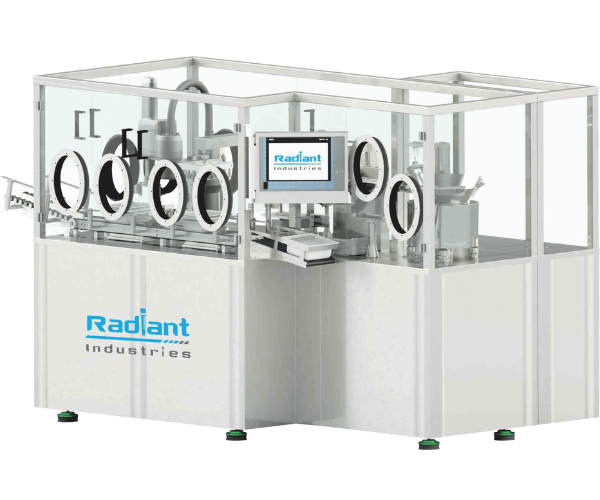
Automatic Tyvek lid removal and inner liner removed by the robotic arm. Empty PFS nest pick and place it on the filling station by the robotic arm. The liquid Filling and rubber stoppering process is done at the same time. Easy access to the individual station because of the Narrow machine’s compact design.
The machine exhibited at Interpack will have the tub opening (by means of a robotic peeler) and syringe filling/stoppering phases integrated all in one unit.Â
Once loaded on the machine The tub moves under the opening station where a robotic arm peels off the external Tyvek lid and removes the internal protective film, discharging them onto a recovery extractable bin. The same robot transfers the open Tub on the load belt of the filing and stoppering unit.
Just one isolator (or RABS) protects both zones but still separates them with vertical laminar air flows and individual pressure control on each area, to guarantee a correct pressure cascade typical of an aseptic filling process.
The isolator and the machine are sanitized by Vaporization of Hydrogen Peroxide (VHP). The VHP technique minimizes sterilization and aeration time.
Special focus
The heart of the machine: a new high-tech arm that moves just like a human hand
The robot that has been integrated in the new syringe filling unit is the outcome of research activities carried out by the Radiant Industries to innovate the automatic machinery industry.
Both the mechanics and software of the Tub de-liding head have indeed been developed entirely by the R&D team with the aim of devising a specific robotised system capable of handling the product with outstanding efficiency in sterile conditions. Since it has been purpose-designed for this function, the robot has been given a futuristic gripper that moves just like a human hand. The software is also incredibly effective in moving it and performing the various consecutive operations:Â
Phase 1Â – handling: the robot get the tub and puts it into position;
Phase 2Â – look for peel-off corner: this phase has been studied to mimic human hand movements. The robot looks for the corner of the lid to be lifted, also, or especially if the corner is folded or bent, and grasps it to gently remove the entire lid without tearing;
Phase 3Â – peeling: the robot peels off the outer lid and throws it into the dedicated bin;
Phase 4Â – remove second protective cover from tub: the robot uses its vacuum cup to get the second cover of the tub, removes and throws it into the collection bin;
Phase 5Â – handling: the robot gets the tub again and carries it to the load conveyor of the filing unit.
Technical Specification :
System | TYVEK REMOVER | Filling Pump/Peristaltic Pump | Closing | Heads | Speed |
|
---|---|---|---|---|---|---|
RI/PFS/AUTO/ROB | ROBOTIC | ROBOTIC AUTOMACIT | ROBICIT/Rotary Piston Pump/Peristaltic Pump | Bunging /Vacuum | 10/5/2 | 6500-7200/3500-4500/1200-900 |
RI/PFS/AUTO/MIC | Mechanical | MECHANICAL AUTOMATIC | Rotary Piston Pump/Peristaltic Pump Rotary Piston | Bunging /Vacuum | 10/5/2 | 5000-6000/2500-3000/1200-900 |
RI/PFS/AUTO/VAC | Mechanical | MECHANICAL AUTOMATIC | Rotary Piston Pump/Peristaltic Pump | Bunging /Vacuum | 10/5/2 | 5000-6000/ |
Optional Accessories :
- In line Check weighing system
- CIP/SIP System
- Nitrogen Flushing
- IPC With 21 CFR part 11 compliance (scada system)
- Filling is also done by robots
- Monitoring and particle counting
Documentation & Qualification
- In pharmaceutical production, Good Manufacturing Practices (GMP) are essential to guarantee that the manufacturing process is constantly controlled according to quality standards, and the drugs can be used safely.
- Therefore, there must be systems to provide documented proof that correct procedures are consistently followed at each step in the manufacturing process, ensuring clarity and traceability of the product quality data acquisition.
- At RADIANT INDUSTRIES, we defined specific actions to ensure that our document management, which we call GDP (Good Documentation Practices), fulfills this objective.
- Document management starts with the client’s specifications (URS) which help us understand the customer’s needs and define the machine’s configuration accordingly. The required machines’ functionality will be tested later during the qualification tests.
- The whole process is described in the picture below, showing the comprehensive Qualification Project Plan (QPP) that covers from mechanical assembly to software and control configuration:
COMPLETE SOLUTIONS FOR PRE-FILLED SYRINGE
PRODUCTION LINE BY RADIANT
INDUSTRIES
